Proving Older Products Are Defective
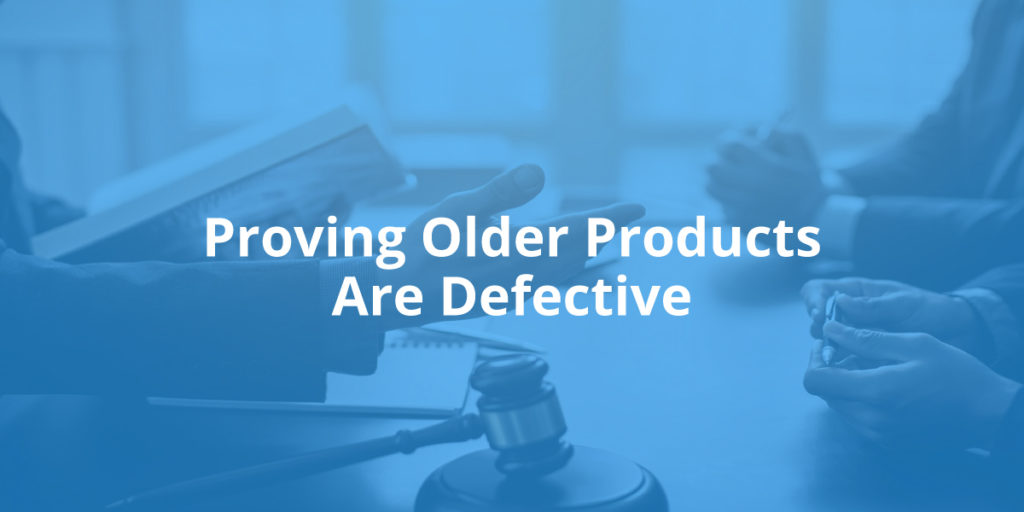
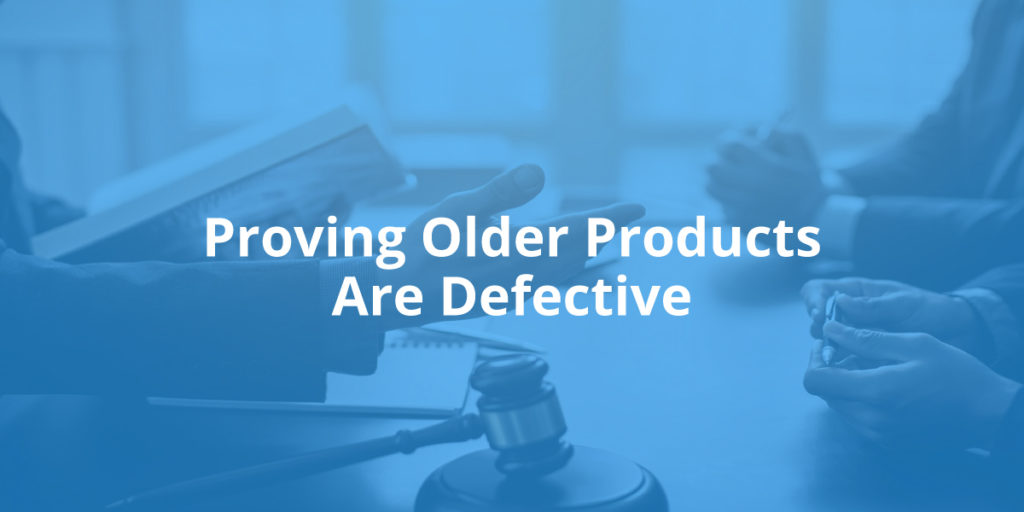
Proving older products are defective in a product liability case can be difficult. However, it is possible with the right arguments. The key to any such case is showing that the product was defective at the time it was designed or sold. Evidence that safer alternative designs were available when the product was designed, manufactured or sold is vital in proving the product was unsafe for its intended use.
Product liability attorney John Mattiacci has successfully litigated product liability cases. Often these cases involved products that were designed, manufactured and sold decades before they caused an accident. Several of these cases resulted in multi-million dollar recoveries.
In one such case, John litigated a case for a client seriously injured by a piece of construction equipment. The equipment was designed, manufactured and sold in the 1980s. The product caused an accident more than 20 years after it was first sold. In the interim, the product was not maintained by its owner according to the manufacturer’s instructions. The user, who was not the owner, was seriously injured when the machine unintentionally activated. The safety interlock that was supposed to keep the machine from activating was broken. The machine was dangerous because it could still operate even though the safety interlock was not working. This created a hazard to operators. The operator, in this case, was crushed and horribly injured.
The key to success is exhaustive research
That case presented several serious challenges. The first major issue was proving that a product that had been in use for more than twenty years was defective when it had not caused a prior injury and was designed with a safety interlock. The second challenge was proving liability when the machine had not been maintained as it should have been by the owner. Third, there was evidence the owner of the machine had attached an unapproved device to the machine. This allowed the defense to argue the machine had been altered by the owner. The use of an unapproved attachment was problematic and gave additional ammunition for the defense to contest liability.
With regard to the first issue, Pennsylvania does not bar cases against manufacturers and sellers of products simply because they were sold years prior to an incident. In this case, John performed exhaustive research of the designs used by the defendant’s competitors back in the 1980s. That was when the defendant’s machine was designed and sold. John found alternative safer designs that were practical, affordable and were in use in the 1980s. John pored over archived patent applications and grants, spoke with former engineers that worked for the defendant’s competitors in the industry, and found and reviewed old product manuals and repair texts that were purchased online in order to find this information.
Using this extensive research, John was able to show that defendant was not using the safest design at the time the defective product at issue was made and sold. Specifically, John was able to show alternate designs in use by other manufacturers that used more robust and reliable safety interlocks. Furthermore, John was able to provide an alternate design that would have made the defendant’s product fail-safe. In other words, John and his experts showed that the interlock on the defendant’s machine could have been designed so that if the interlock broke, the machine would be unable to work at all. This alternative design was developed specifically for the machine that was involved in the accident. This alternate design was safer in that it would in turn force the owner to repair the interlock in order to use the machine. This was infinitely better than the defective design used by the defendant, which allowed the machine to continue to function even when the safety interlock that protected the operator had broken.
Ultimately, John showed that the construction equipment should have had safety features that adequately protected the operator and were fail-safe. The evidence showed the defendant’s product was not fail-safe. John proposed safer, alternative designs that were feasible and cost-effective. Most importantly, the safer design was technologically feasible to enact in the 1980s when the defendant’s product was sold.
This fail-safe argument was extremely effective. If the defendant’s machine had been fail-safe, the machine would be disabled completely when the safety interlock broke. The equipment only would have worked after the safety interlock was completely repaired. This was incredibly important in showing the defendant’s design was unsafe and in proving the plaintiff’s claims.
John also showed that the lack of maintenance by the owner was not the root cause of the accident. This went hand-in-hand with showing that the design of the machine was unsafe because it lacked an interlock that was fail-safe. Ultimately, John showed that the proposed safer alternative design would negate the owner’s failure to maintain the machine. By incorporating the fail-safe design advocated by John, an owner would have no choice but to fix the safety interlock or else the machine would not work at all. This would be much safer than the defendant’s design, which allowed the machine to operate even when the interlock had broken. The defendant’s design did not give the machine’s owner an incentive to fix the machine’s safety features, as long as the machine still worked.
With regard to the unauthorized attachment, John was able to find evidence that the use of the attachment should have been reasonably anticipated by the defendant. John performed an extensive search to show that the attachment was advertised in trade magazines and publications to which the defendant subscribed or read. Additionally, John was able to show that the defendant attended the same trade shows where the attachment was displayed or advertised. Accordingly, there was evidence that the defendant knew or should have known that the “unauthorized attachment” was being advertised for use on the defendant’s product for years prior to this incident.
Showing that the defendant knew or should have known about the use of the attachment was vital. This is due to Pennsylvania’s law regarding the alteration of products. A product that has been significantly altered from its original design may allow a defendant to escape liability. However, the Superior Court stated that in determining whether a product was altered there must also be an analysis as to, “whether the manufacturer could have reasonably expected or foreseen such an alteration.” See D’Antona v. Hampton Grinding Wheel Co., 225 Pa. Super. 120, at 125 – 126; 310 A.2d 307; 1973 Pa. Super. LEXIS 1491. Here, John was able to show that the defendant could have reasonably expected that this attachment would be used on defendant’s products. This was accomplished by showing that the unauthorized attachment had been advertised for use on the defendant’s machines for years. The evidence showed that the defendant knew or should have known of these advertisements.
The lessons learned from handling cases involving older products are simple. Dig for information to find the safer, alternative design that was available when the defendant’s product was designed, made or sold. Do not rely solely on experts. Never rely upon the defendant to give you the information you will need to prove your case. Be willing to track down people who worked on these products for competitors and ask them questions. Do your own research, scour patents, order old manuals online, and keep in mind that a machine that utilizes a fail-safe design is infinitely safer than one that does not.
Contact product liability attorney John Mattiacci today if you or a family member has been injured by a defective product. We are here to help.